Optimizing your existing products to maintain a competitive edge in today’s market
At EDS International, our main objective is to help you optimize existing products through design and manufacturing process improvements, with the goal of enhancing performance, reducing costs, and resolving any design or performance issues.
Our team of experienced professionals will work closely with you to identify areas where your products or your production processes can be enhanced. Whether it’s reducing manufacturing or assembly costs, obtaining more competitive pricing, or extending product life, we have the knowledge and resources to guide you through the optimization process.
If you have an outdated product or if you are simply trying to improve or make it more cost-efficient, EDS International partners with you to modernize it.
Listed below are some basic objectives for pursuing design optimization.
- Reduce manufacturing or assembly costs
- Obtain more competitive pricing
- Extend product life
- Solve previously identified design, manufacturing or performance issues
- Enhance performance and functionality
- Increase attractiveness or appeal
- Enhance sales
- Perform Design For Manufacture (DFM) – for product development
By making even minor changes or adjustments it is possible to efficiently optimize a product. The goal is to identify which characteristics of the product require optimization and what issues will be resolved.
Types of Product Optimization:
There are two types of product optimization:
- Design (feature) optimization – is about identifying the features of the product which can be improved and changes made to facilitate the manufacturing process and/or improve the performance of the product. The two most widespread areas of design optimization are component and material optimization. During material optimization, EDS will identify the right material for the product by comparing material properties and manufacturing processes. And component optimization is required when a root cost analysis determines that a specific component or a component set is responsible for decreasing product performance.
- Manufacturing Process optimization – depending on the manufacturing processes used, there are limitations on design. A design for Manufacturing (DFM) study should be performed to guarantee that the product is suitable for the production process or technique used to design and produce it. For example, Mold Design Optimization or Assembling Line Optimization can be pursued.
Any of the above-mentioned product optimization steps can make a significant difference to your product and your business and bring it to the next level.
Product Optimization Process:
Regardless of the type of product optimization chosen, EDS consistently employs a six-step optimization approach. The image provides an overview of the process along with a detailed description of each optimization step below.
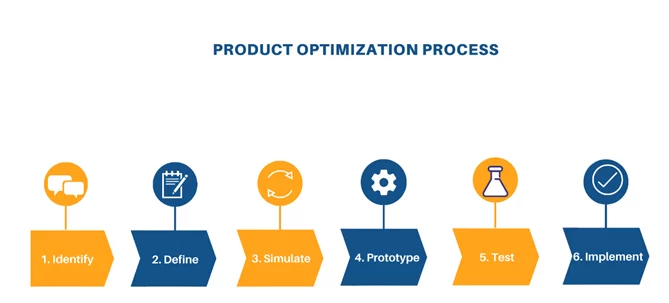
- Identification – Once the product challenges are understood, we will identify the features and processes to be improved. Optimization is not limited to manufacturing but also include design, testing, and transportation. In any case, the relevant industry standards will be applied to any features and/or process chosen for improvement.
- Definition – EDS defines which methods are to be applied to achieve the optimization objective. For example, for a feature improvement such as weight reduction, we could consider material, stress,or topological optimization. If optimization will be applied to a process then a different approach would be considered. For instance, to achieve a more efficient distribution, we could consider packaging optimization.
- Simulation – At this stage, we perform calculations and simulations. Simulations are used to estimate the impact of the optimization proposals and methods defined previously, make a comparison of their impact, and select the best fit based on the criteria defined during the Identification and Definition stages.
- Prototype – Pilot – If the result of the simulation was a modification to the product (i.e. feature) then a new prototype needs to be built. However, if the result of the simulation was a modification to a process then a production batch would have to be completed utilizing the new process.
- Testing – In both cases, after the prototype is built or the production batch is completed, the next step is to test the results. The new features and associated product must withstand rigorous testing and the results of any process changes must be corroborated with the expected process improvements. Multiple prototypes or batches could be required depending on the testing results.We recommend testing only one feature or process change at a time to avoid difficulty identifying which changes have caused testing variations.
- Implementation – If the results from the simulation, prototyping, and testing phases are positive, it’s time to move to full production. At this time all changes to cost, lead time, and resources will be defined based on the results from previous phases.A plan for full production life-cycle implementation consisting of manufacturing schedules, facility modifications required, tooling purchasing, tooling adjustments, workers training, documentation updates, testing plans will be presented and agreed.
Product Optimization at EDS International
For the last four decades, our technical team has been optimizing products for our clients from our local offices in China, India, and the U.S.
Our R&D department in Ningbo, China specializes in product analysis to ensure products comply with relevant market requirements. Our specialized design optimization services concentrate on enhancing features, materials, and components, thereby ensuring that your products effortlessly meet the highest benchmarks of both quality and functionality.
With our presence in various regions, including China, South East Asia, and North America, we offer global support to clients seeking product optimization. Our on-the-ground engineering teams assist in the development, prototyping, production, and inspection of parts, ensuring seamless collaboration and quality control.